Zamac perfume cap wholesale | How to make the zamac perfume cap so beautiful? The key is the surface treatment.
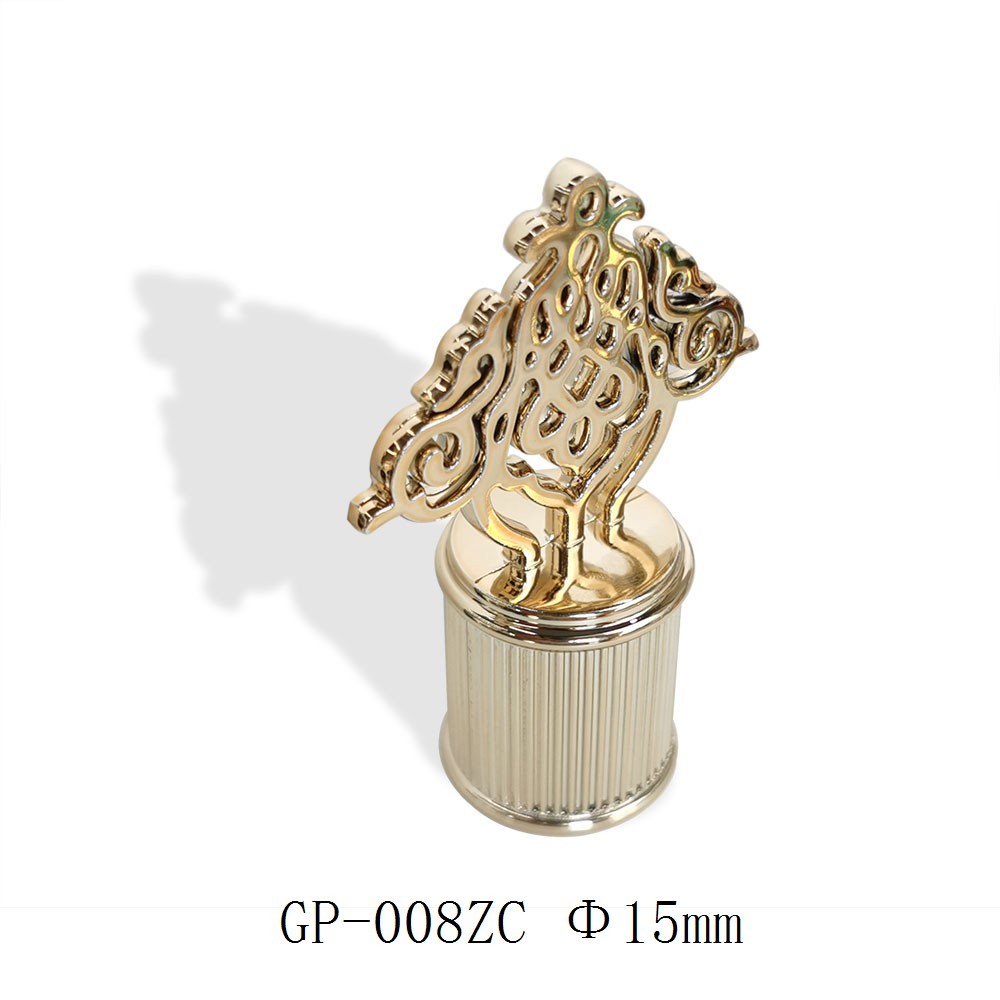
Electrophoresis
Used for stainless steel, aluminum alloy die-casting parts, zinc alloy die-casting parts, etc., can make the product show various colors, and maintain the metallic luster, at the same time enhance the surface performance, and have better anti-corrosion performance.
Process flow: pretreatment→electrophoresis→drying
advantage:
1. Rich colors;
2. No metal texture, can be used with sandblasting, polishing, wire drawing, etc.;
3. Processing in a liquid environment can realize surface treatment of complex structures;
4. The technology is mature and can be mass-produced.
shortcoming:
The ability to conceal defects is average, and electrophoresis for die castings requires higher pre-treatment.
PVD vacuum plating
The full name is physical vapor deposition, which is an industrial manufacturing process that mainly uses physical processes to deposit thin films. All kinds of zinc alloy die castings and aluminum alloy die castings can be vacuum electroplated.
Process flow: cleaning before PVD → vacuuming in the furnace → washing target and ion cleaning → coating → coating finished, cooling out of the furnace → post-processing (polishing, AFP)
advantage:
1. It can be made in various colors, such as flashing silver, magic blue, crack, drop silver and other seven colors;
2. The coating uses a wide range of materials, which is easy to meet environmental protection requirements;
3. Vacuum electroplating can reach 200℃, and parts used in high temperature parts can be vacuum electroplated.
shortcoming:
If UV oil is not used for vacuum plating, its adhesion is very poor, and it cannot pass Hundred Test. In order to ensure the adhesion of vacuum plating, special spraying treatment is required afterwards, and the cost is of course higher.
Electroplating
Electroplating is a technology that uses electrolysis to attach a metal film to the surface of the metal to prevent corrosion, improve wear resistance, conductivity, reflectivity, and enhance aesthetics. Electroplating technology is widely used in Many zinc alloy die castings and aluminum alloy die castings can be applied.
Process flow: pre-treatment→cyanide-free alkali copper→cyanide-free copper-nickel alloy tin→chrome plating
advantage:
1. The coating has high gloss and high-quality metal appearance;
2. The base material is SUS, Al, Zn, Mg, etc.; the cost is lower than that of PVD vacuum plating.
shortcoming:
Environmental protection is poor, and environmental pollution risks are greater.
Spray paint
Spray painting is the use of compressed air to disperse liquid paint (commonly known as paint) into paint mist particles that adhere to the surface of zinc alloy materials. It is the name of the surface coating process of industrial products. Oil injection processing includes plastic injection, silk screen, pad printing; EVA, rubber and other shoe materials color change, silk screen. According to customer requirements, products such as high temperature resistance, friction resistance, UV resistance, alcohol resistance and gasoline resistance can be produced.
advantage:
Painting can make monotonous products look more beautiful after being sprayed with various colors. At the same time, because of the extra layer of protection, it can also extend the life and service life of the product.
shortcoming:
If the surface of the product is rough, the spray paint cannot be leveled; the friction resistance is relatively not very good.